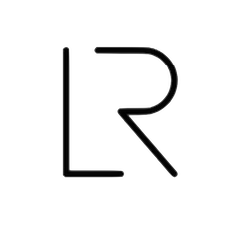
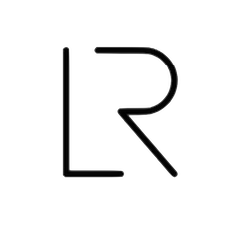
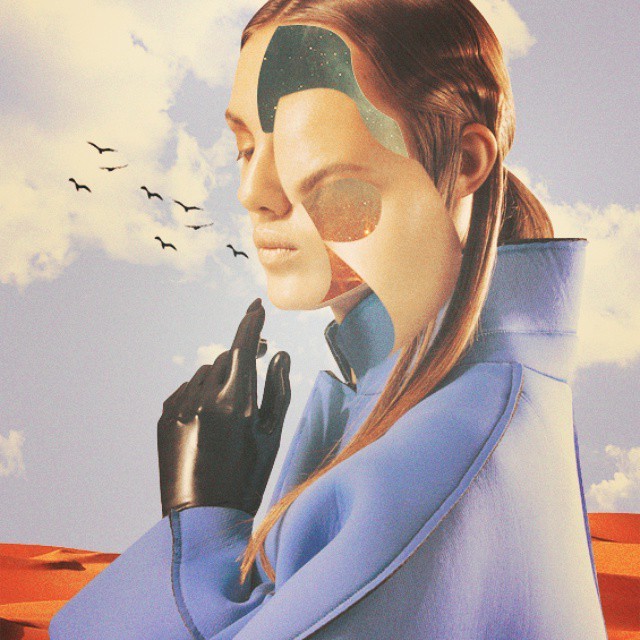
The Rise of Carbon Fiber
Why the space-age material may finally come to earth.
By Luke Renner | Published April 5th, 2018 | Canonical
In 2010, Japan caught the manufacturing and automotive spotlight when materials producer, Toray Industries, announced that they had finally developed a process to allow carbon fiber to be used for mass-produced auto bodies. Up until then, Carbon Fiber had been slanderously expensive — about twenty times the price of steel. Toray’s technology dropped the cost by a fourth — to about five times the cost of steel.
For decades, industry experts have carried a torch for the space-age material due to its unprecedented lightness and strength. Car manufacturers see carbon fiber as a path to highly fuel efficient and safe vehicles. Architects imagine buildings that could rise to twice their current height. Aerospace engineers see carbon fiber as a material that will drive us further and further beyond earth’s orbit — perhaps even to Mars.
The Toray news marked a dramatic acceleration in the rise of carbon fiber. Though materials experts had known of it for decades—we even used it in on the moon—its high manufacturing costs have thus far prevented Carbon Fiber from rising to the level of mass production.
For Toray Industries, the last eight years have been a river of good news as major vehicle manufacturers like Toyota, Honda, and Nissan have lined up to partner with the manufacturer. For the rest of industry, the race continues with startups all over the world clamoring to develop and patent new methods to drop the price of carbon fiber even further.
A Primer on Carbon Fiber
Carbon Fiber is a fabric-like material that is built of carbon atoms bonded together to form long, microscopic strings. These strings are extremely durable, light and manufacturers can braid them into threads, woven into meshes and/or combined with resins and plastics to produce excellent building materials.
Carbon fiber offers lots of benefits over traditional materials. For one, it is considered chemically and thermodynamically stable, which means it won’t react to the outside environment and corrode like iron or bronze. Depending on its particular construction, carbon fiber can be ten times stronger than steel.
In short, carbon fiber is an excellent material. It’s both stiffer and lighter than almost any other material we know of. Additionally, manufacturers can finely control carbon fiber’s stiffness. Unlike metal, carbon fiber’s stiffness properties apply unidirectionally, which means manufacturers can carefully layer and rotate each strand to add flexibility when needed. Imagine constructing a building using a material as strong as steel but flexible enough to survive an earthquake.
Clearly, Carbon Fiber is a fantastic candidate for wide-spread use as a material, which is why Vehicle Manufacturers are so interested. However, the leading consumer of carbon fiber is the aerospace industry, which already uses 30%of the global supply of carbon fiber.
We are already starting to see Carbon Fiber in more places. The general framework is that any product that needs to be (a) strong and (b) light is a good candidate for use.
So far bike helmets, golf clubs, missiles, artificial limbs, and even robots have all been constructed with the material. These products remain expensive, however. A carbon fiber bike helmet, for example, is about ten times the cost of a regular helmet.
In addition to being strong, Carbon Fiber is also radiolucent, which means that it doesn’t show up on X-Rays. For the med-tech industry, this is helpful because companies can use it to construct MRI machines or prosthetics.
The Race to $5
Right now, the process for creating Carbon Fiber is proprietary with different manufacturers producing the material via different recipes. To be sure, the manufacturing process is complicated, involving many stages and lots of nasty chemicals. However, the general recipe boils down to applying a huge amount of heat to a chemical swill in order to burn off all of the non-carbon molecules.
Thus far, the manufacture of carbon fiber is expensive and energy-intensive, which is why there are industry-wide efforts to reduce costs. The carbon fiber holy grail is to bring its cost down from its current price of about eight-to-ten dollars per pound to five dollars per pound, which is the unit costs many industry experts cite as the threshold for widespread commercial viability.
One opportunity to reduce costs lies in the chemical swill itself. Carbon Fiber is typically made from polyacrylonitrile (PAN), which is both pricey and nonrenewable. According to Jinxue Jiang, a postdoctoral fellow in the Ahring laboratory at Washington State University, PAN can contribute about half of the total cost of production of Carbon fiber. He and his team are investigating the possibility of adding lignin, a component of plant cell walls to the swill to reduce costs without reducing strength.
Even the Department of Energy is getting involved in the race to five dollars per pound, offering clean energy companies a lab in which researchers can develop less expensive, better-performing carbon fiber materials via novel manufacturing processes. In addition to being a research lab, the facility will produce up to 25 tons of carbon fiber per year in order to help enable the large-scale manufacturing of carbon fiber products.
The Carbon Fiber Footprint
Even if companies can reduce the cost to manufacture carbon fiber, the environmental impact of the material will remain. As mentioned, a huge amount of heat is necessary to burn off the non-carbon molecules in the chemical swill. Each aspect of this process—namely (a) creating heat and (b) burning off non-carbon molecules—represents an environmental cost.
In the case of the former, energy is expensive and manufacturers must use a massive massive amount of it to bring internal oven temperatures to the thousands of degrees necessary to force this chemical process. In the case of the latter, non-carbon molecules are industrial pollutants and must be carefully—not to mention, expensively—disposed of.
Worse yet, developers cannot easily recycle Carbon Fiber, which is a problematic departure from other reusable materials such as aluminum.
To maximize the strength of a carbon fiber mesh, its nano-strings must be woven into a precise pattern— and then that pattern is locked into place using polymer or plastic. To extract the nano-strings for reuse, recyclers must somehow melt away the polymers and then re-thread the fibers into a new mesh. Every step in this imprecise process reduces the strength and durability of the resulting material.
These days, some second-hand carbon fiber makes its way to consumer goods like golf clubs, where relative lightness is more important than its strength.
However, most of it is discarded.
Investing in Carbon Fiber
To be sure, the firms that can figure out how to reduce the costs of carbon fiber and/or optimize its reuse may well be the ones to finally turn this promising material mainstream.
Similarly, investors are looking to new companies who have demonstrated progress in cracking the carbon fiber code. Regardless of when the industry hits that so-far mythological five dollars per pound price point, global demand for carbon fiber continues to rise. In the last eight years, demand has risen from 33,000 metric tons in 2010 to 70,000 metric tons last year.
Keep Reading
Have you felt the frustration? Logging into your Indeed candidate pool, only to be let down? Mediocre cover letters. Mediocre work experience. Mediocre candidates. If it sounds familiar, you aren’t alone.